What is Lean Six Sigma and How You Can Apply It
Organizations are only as strong as their processes. After all, they run thousands of them.
Process improvement has long been top of mind for all companies across industries to improve efficiency, reduce costs, and deliver greater value. Process improvement by itself, however, is simply a buzzword—it needs a structural and strategic approach to achieve the ends it’s supposed to.
One of the most popular approaches to achieve operational excellence and continuous process improvement is Lean Six Sigma.
In this article, we dive into what Lean Six Sigma is and how you can apply it in your organization to achieve the efficiency, cost reduction, and better customer experiences you need to stay competitive.
What is Lean Six Sigma?
Lean Six Sigma is a process improvement approach that marries elements of Lean and Six Sigma.
The Lean methodology rose to prominence in the manufacturing sector, specifically at Toyota. Its focus is improving manufacturing and transaction processes by removing waste to deliver better value to customers.
Six Sigma is a quantitative approach to process improvement with a set of quality controls to minimize errors and process variance while improving execution times. It was born in the 1980s to improve execution quality and speed by reducing errors and defects in processes.
Therefore, Lean Six Sigma is a hybrid of the two process improvement approaches that borrows elements from both to standardize processes, remove waste, and reduce errors to increase execution times of processes and the value delivered to customers.
How to Apply Lean Six Sigma in Your Organization
Applying Lean Six Sigma to your continuous process improvement initiatives follows five simple steps:
1. Definition
In the first stage of Lean Six Sigma– the definition phase – you identify and define the problem with your process. Business process analysis (BPA) is critical in this initial phase.
An assessment of your process with the aid of a solid BPA solution will help you isolate whether it’s redundancy, variance, errors, or slow execution times preventing optimal efficiency and quality.
2. Measurement
In the second phase of applying Lean Six Sigma to your continuous process improvement efforts, the problem is quantified. Again, robust process analytics and insight enable the quantification of value being delivered or lost.
Quantifying the problem contextualizes how much money is being lost by long execution times, errors committed that could be avoided, or different flows to execute the same process.
3. Analysis
Once the problem has been identified and quantified, it’s time to analyze the cause of the problem. In other words, what’s wrong with how work is being done.
Are there redundant steps in the process that could be removed to streamline the workflow? Are there steps that are prone to error? Where are processes deviating from the standard model, and why?
A good business process modeler is paramount in the analysis phase of Lean Six Sigma. Additionally beneficial is a centralized location where all processes can be stored and collaborated on, instead of using siloed tools that introduce complexity and bottlenecks to your process improvement efforts.
Even more powerful is a Business Process Analysis solution that delivers predictive and simulation capabilities so you can manipulate the process with different variables and see where the problem and solution might be.
4. Improvement
In this phase of the Lean Six Sigma application, the improved business process is implemented according to the process improvement strategy that was chosen, whether it be modernization, optimization, standardization, or automation.
5. Control
In the final stage, the improved process is closely monitored and continually assessed, ensuring it delivers increased value via better output quality or quicker execution times.
As a continuous improvement strategy, Lean Six Sigma is exactly that—continuous and an ongoing process for cyclical improvement.
That same process is meant to be closely tracked, revisited at a regular cadence, and have the same fives steps applied to it, so the needle is always pushing towards operational excellence and perfection.
Share this
Recent Stories
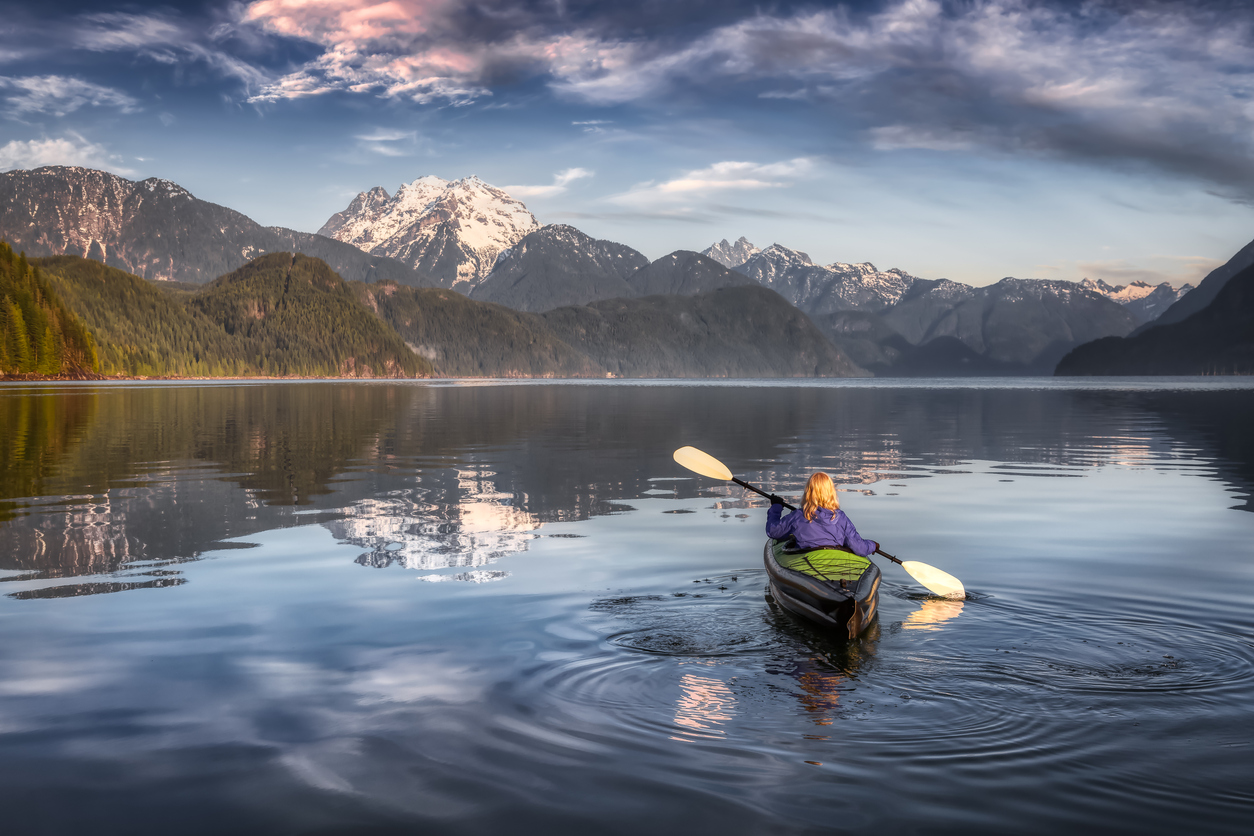
What is Value Mapping: Everything You Need to Know
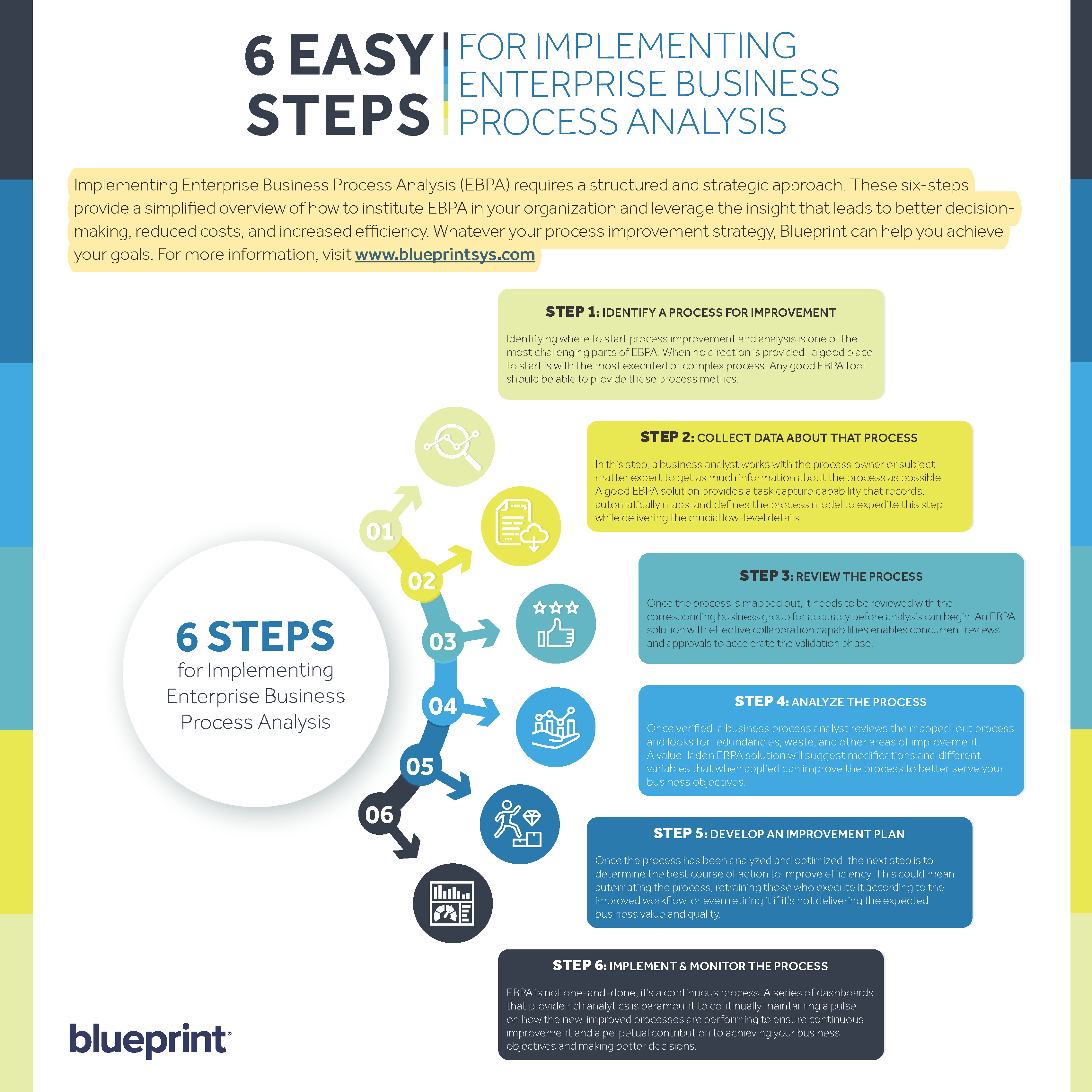
INFOGRAPHIC: 6 Easy Steps for Implementing Enterprise Business Process Analysis (EBPA)
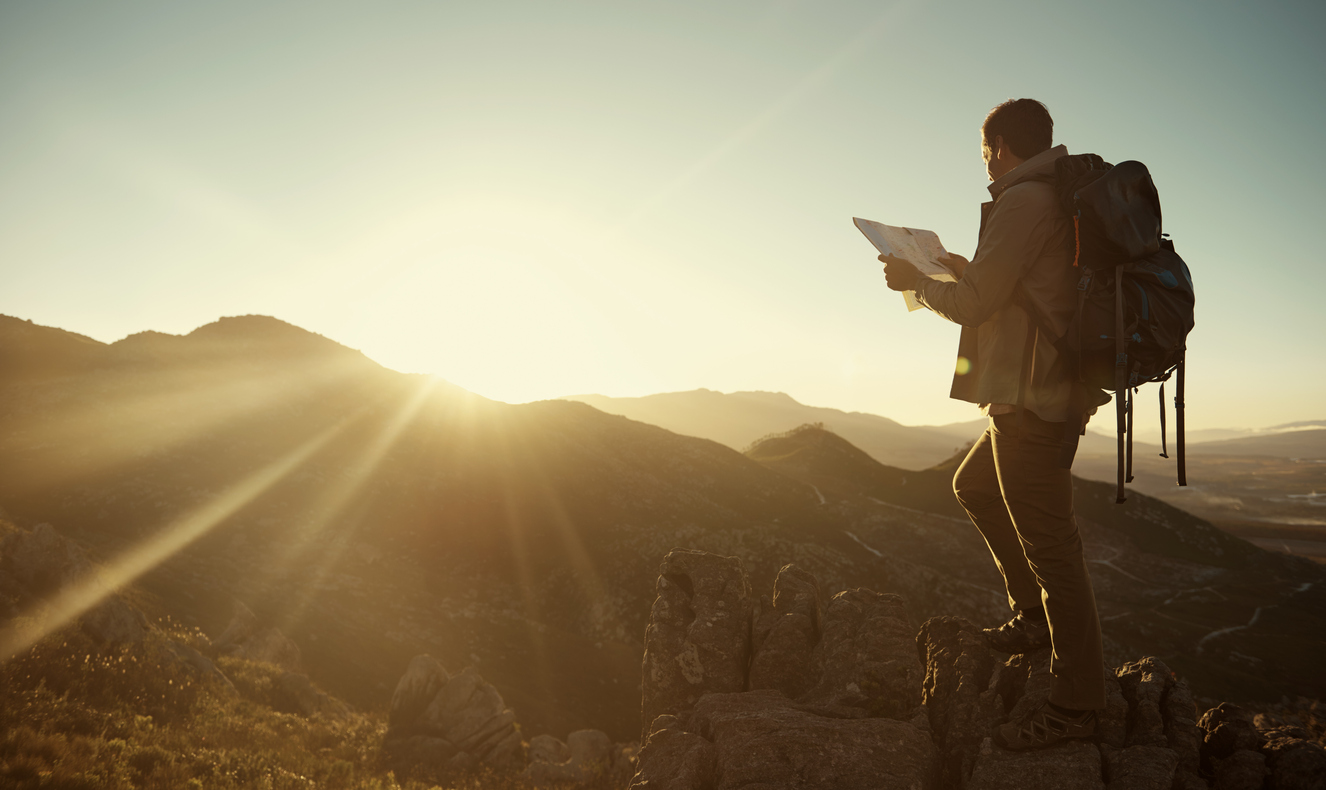