Why Business Process Analysis is So Important for Successful Automation
Organizations are experiencing automation overload. To realize all the benefits that automation promised, there was a mad dash to automate all the low-hanging fruit and quick wins possible.
Business process mapping and business process analysis (BPA) should always come first before automation is even considered, yet (BPA) was overlooked in favor of trying to leverage all the cost savings, efficiency gains, and increased quality that automation’s value was built on.
Organizations didn’t understand their business processes; they didn’t fully understand how work was being done, yet chose to automate that work anyways, which has been severe and damaging.
The Consequences of Not Modeling and Analyzing Your Business Processes Before Automation
The reason companies raced to automate everything they could is understandable. Automation is a significant investment, and adopters needed to deliver tangible results to the program’s sponsors in the form of returns.
What that approach has led to, though, is constant break-fix cycles, maintenance headaches, and automation outages that cost more money than the value being delivered.
Organizations automated what they shouldn’t have and left aside what probably should have been automated. They also didn’t bother to improve their business processes by eliminating waste before automating them.
When you automate flawed processes or the wrong ones, you’ll eventually leave yourself fighting fires or losing money and having to start again—a scenario many organizations find themselves in. This unfortunate reality is a consequence of not applying business process modeling and analysis as the first step to any automation initiative.
Why Business Process Analysis is Critical to Automation
For process automation to deliver meaningful results, you need to understand what’s happening in a process before automating it; you need to assess a process and understand whether automation makes sense.
If cost reduction and increased efficiency by way of higher quality and fewer errors is the objective, processes can be vastly improved without having to do any automation, saving you money and precious resources.
Anecdotally speaking, 75% of process improvement doesn’t involve any automation. For example, take a process where automation can decrease execution time by 80%. If there are only 10 inputs a day, the return on investment you’d realize by automating that process becomes negligible because the output remains the same whether it is executed manually or via a bot.
That’s why business process analysis is so integral to automation. There would be no other way of knowing that without analyzing that process first. You need to quantify and map the value of processes before determining the best process improvement strategy, whether that be automation or something else.
There’s no better solution that can help you quantify the value of your processes than Blueprint.
Blueprint offers a Value Mapping Assessment service that delivers a comprehensive analysis of your entire automation estate so you can stop fighting fires and understand how to improve specific automations to maximize their value and increase their resiliency.
Blueprint’s Value Map Assessment provides detailed, actionable recommendations for your automation estate as a whole or even right down to individual processes, identifying where there are redundancies, where processes are unnecessarily complex, and provides detailed opportunities for process optimization, re-platforming, reuse, and retirement of inefficient automations.
For example, we were able to identify an automation for one customer that was costing them roughly $1,000,000 to maintain, support, and operate. The same process was only delivering $300K in business value. By retiring that one automation alone and returning it to manual execution, we helped that customer save $700,000.
How much money are your ineffective and inefficient automations costing you?
To learn more about Blueprint’s Value Map Assessment, download the brochure or schedule a free consultation to speak to one of our solutions experts here.
Share this
Recent Stories
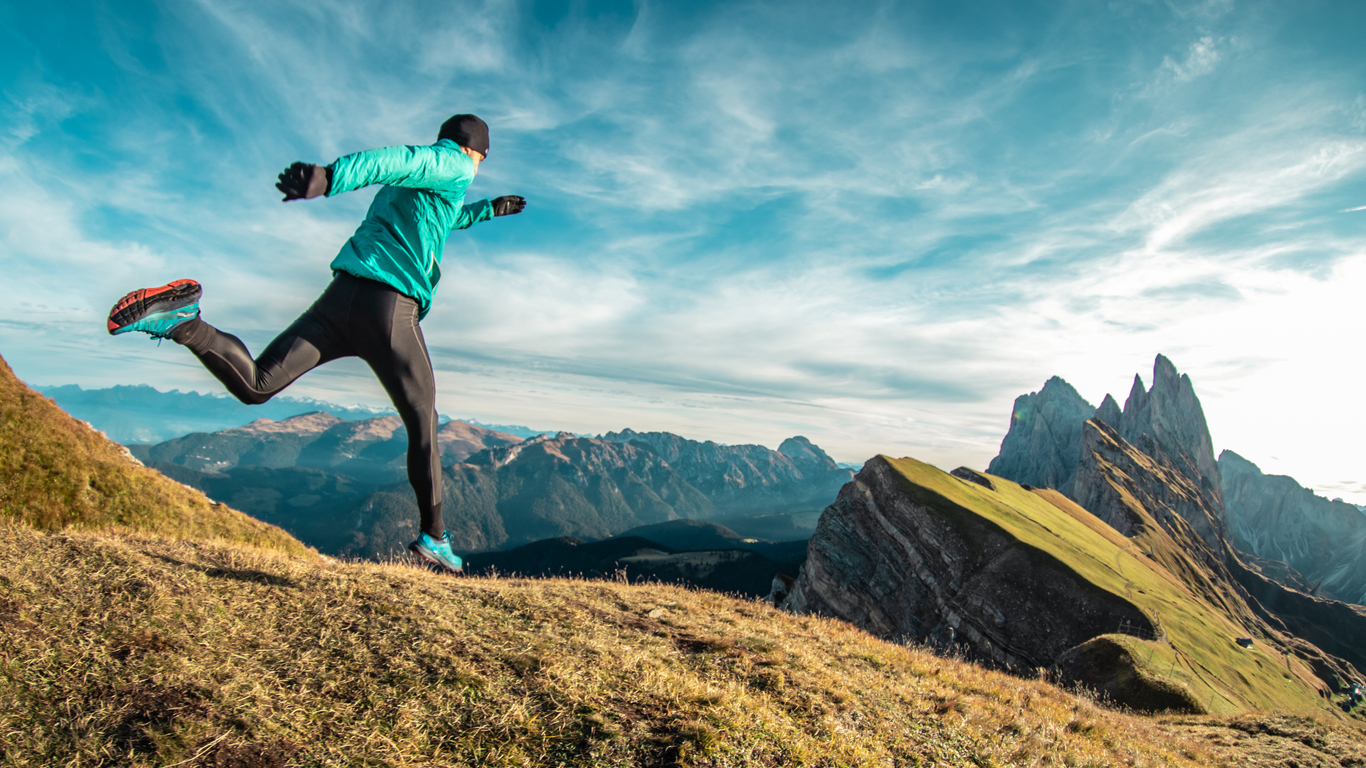
6 Easy Steps to Implement Enterprise Business Process Analysis (EBPA)
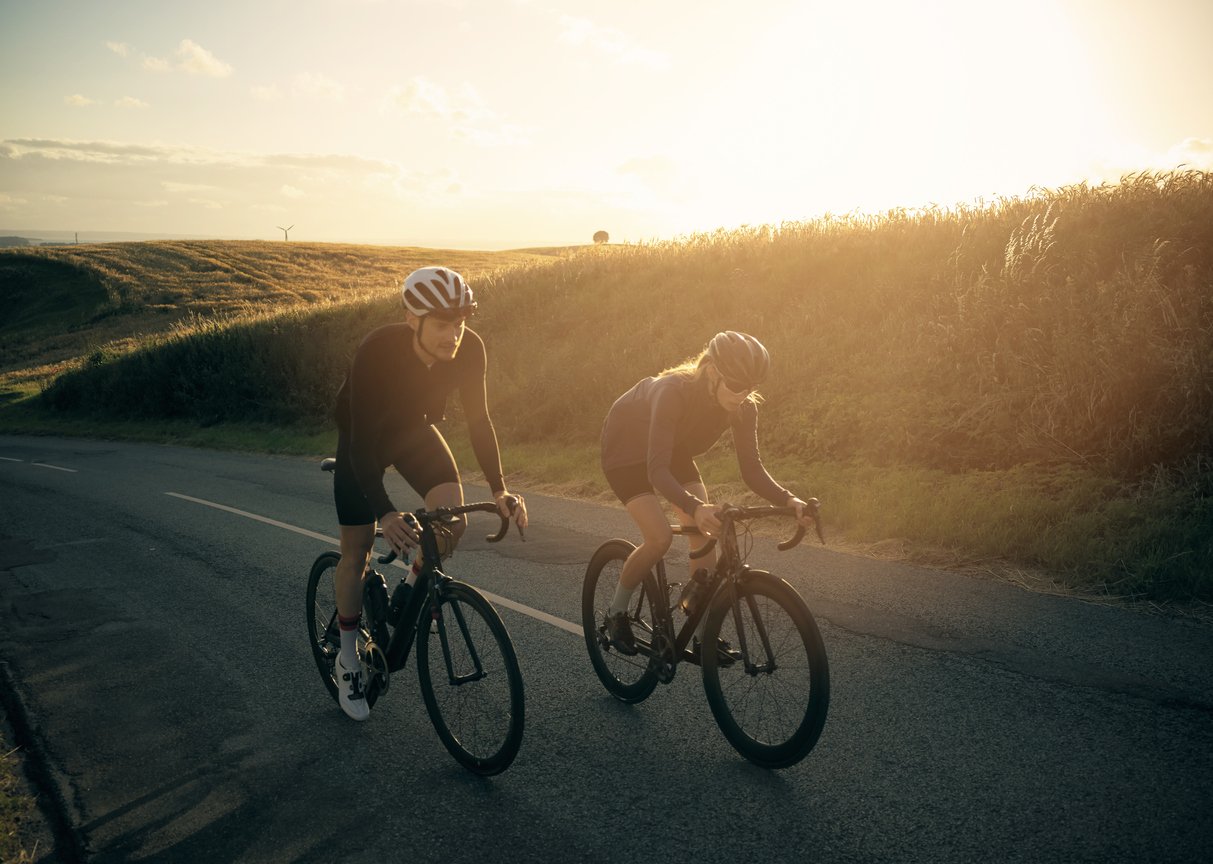
BPA vs. BPM: What’s the Difference?
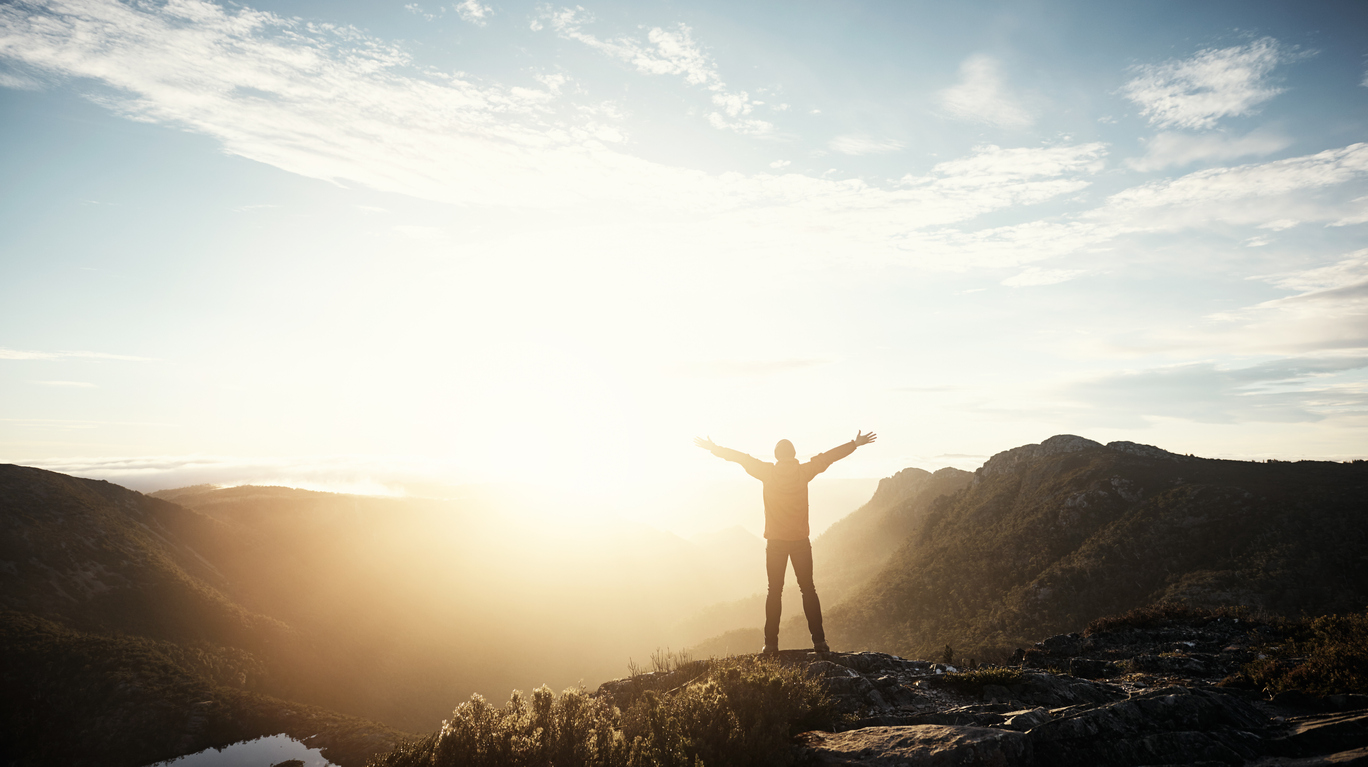