RPA Bot Repair Times: How Long Does It Take to Fix a Broken Automation?
RPA (Robotic Process Automation) maintenance and support are major pain points for all automation programs. When an RPA bot fails, the impact is significant because a business process or task is not being executed, causing an operational disruption, which means lost value and diminished returns.
In this article, we explore the steps involved in fixing broken bots and the factors that impact repair times for broken automations, so you can avoid and mitigate them to minimize down time and value lost from automation outages.
The Steps Involved in Fixing a Broken Automation
When an automation fails and throws errors, there is a series of sequential steps RPA developers must follow before being able to repair the bot and get it back into production. Those steps for RPA bot repair are:
1. Identifying the Cause of the Error
Logically, the first step to fixing a broken automation is identifying what went wrong in the first place to cause the outage. The time required to identify the root cause of the error can vary significantly according to various factors. The most notable factor that influences maintenance effort is the presence or absence of detailed documentation or specifications.
Even simple issues like login failures from password changes can take a long time to identify and diagnose if documentation doesn’t exist because investigating the root cause is just that—a matter of manual investigation that can be quick at times and arduous at others.
More complex issues like errors in logic or integration problems with other systems can take much longer to diagnose because debugging complex code or resolving system compatibility issues is no simple feat. Suffice it to say, identifying the cause of the error is usually the step that takes the longest to resolve when a bot breaks. Depending on the issue, it can take anywhere from a few hours to days and even weeks.
2. Identifying and Defining the Solution
Once the problem and the root cause are identified, the next step involves deciding on and defining the fix. Part of this process is rooted in determining whether the breakage or error can be resolved with a simple tweak or whether a more extensive rewrite of the bot is needed.
Naturally, minor tweaks can be executed quickly, whereas bigger overwrites of the bot’s code may demand more meticulous planning or even the involvement of other departments.
3. Implementing the Solution
Implementing the solution depends on the complexity and size of the fix. If it’s a minor adjustment due to a software update that might have changed the UI (user interface), causing the error, most of the time will be spent investigating the root cause, but the solution is usually a minor fix.
Refactoring code or having to redo a major integration is a whole other story. A more extensive solution like this would require significant testing and quality assurance, not to mention the rewrite of the code to ensure that it works as expected in both the testing environment and production.
4. Testing and Quality Assurance
Whether it was a minor or major fix, testing a repaired bot before it’s deployed into production is critical. Testing and performing the necessary QA (quality assurance) according to your organization’s SDLC (software development lifecycle) ensures your fixed bot performs as expected and doesn’t introduce any new issues that would warrant another outage.
This phase certainly delays the bot from being reintroduced into production; however, it’s necessary to guarantee the long-term viability of that bot and ensure it continues to deliver the value it was designed to.
In terms of testing, unit testing that ascertains that the individual components or fixes of the automation work correctly should be performed and could take a few days.
Integration testing that ensures the repaired bot interacts with other systems correctly extends the timeline to deployment however, this is also an important step that should certainly not be overlooked.
5. Re-deployment and Monitoring
After testing, the repaired automation is ready to be re-deployed into your production environment. At that point, the bot and the rest of our automation estate must be continuously monitored to ensure it’s being executed without errors.
Careful and intentful monitoring right after re-deployment is recommended to ensure it’s working correctly and not throwing any immediate errors. However, a close eye should be kept on it long-term to guarantee optimal performance, longevity, and stability.
While those are the steps and loose timelines to repair an erroneous RPA bot, several factors can impact the timeline for successful redeployment.
The Factors that Impact Fixing and Redeploying Broken Bots
1. Documentation
Automation programs are quickly realizing how crucial documentation and technical specifications are to quickly repair broken bots.
One client we worked with informed us that RPA developers spend at least 30% of their time trying to understand what automations are doing.
Not committing to robust and detailed documentation during the development phase may save a little time but will almost certainly cost a lot more and be much more damaging down the line.
As a rule, 50% of a developer’s time designing and developing a bot should be devoted to producing robust specifications and documentation for several reasons, with agile and swift maintenance being among the main ones.
Learn More: Why Automation Documentation is Essential: 4 Key Reasons You Can’t Ignore
2. Complexity of the Bot
As communicated earlier, the more complex the automation, the harder it will be to identify the problem (especially without documentation if none exists), plan the solution, implement the fix, and test it, thereby elongating the whole process.
3. Team Size
More automation team members mean smaller backlogs of broken automations sitting idly. It also promotes collaboration, enabling team members to receive support and insight to unblock any barriers or bottlenecks should they encounter any.
Conclusion
The repair and redeployment of an RPA bot is a meticulous process that requires a well-coordinated approach to minimize downtime and maintain operational efficiency.
The journey from identifying the cause of a bot's failure to successfully redeploying it involves several critical steps, each demanding careful attention to detail. Key stages include:
- Thorough problem identification (which often hinges on the quality of existing documentation)
- Precise and often creative problem-solving
- Rigorous testing to ensure no further issues arise, and
- Continuous monitoring post-deployment to safeguard against future disruptions.
Documentation is pivotal in expediting these processes, underlining the importance of investing in comprehensive and clear documentation from the outset. Moreover, the bot's complexity and the automation team's size are crucial factors that influence the duration and success of the repair process. Larger teams and simpler bot designs generally translate to quicker recovery times.
Ultimately, the effectiveness of an RPA bot repair process not only impacts the immediate operational capabilities of a business but also its long-term technological resilience. Proper planning, skilled execution, and ongoing vigilance are essential to leveraging the full potential of RPA and ensuring that these digital workers contribute positively to business outcomes.
Share this
Recent Stories
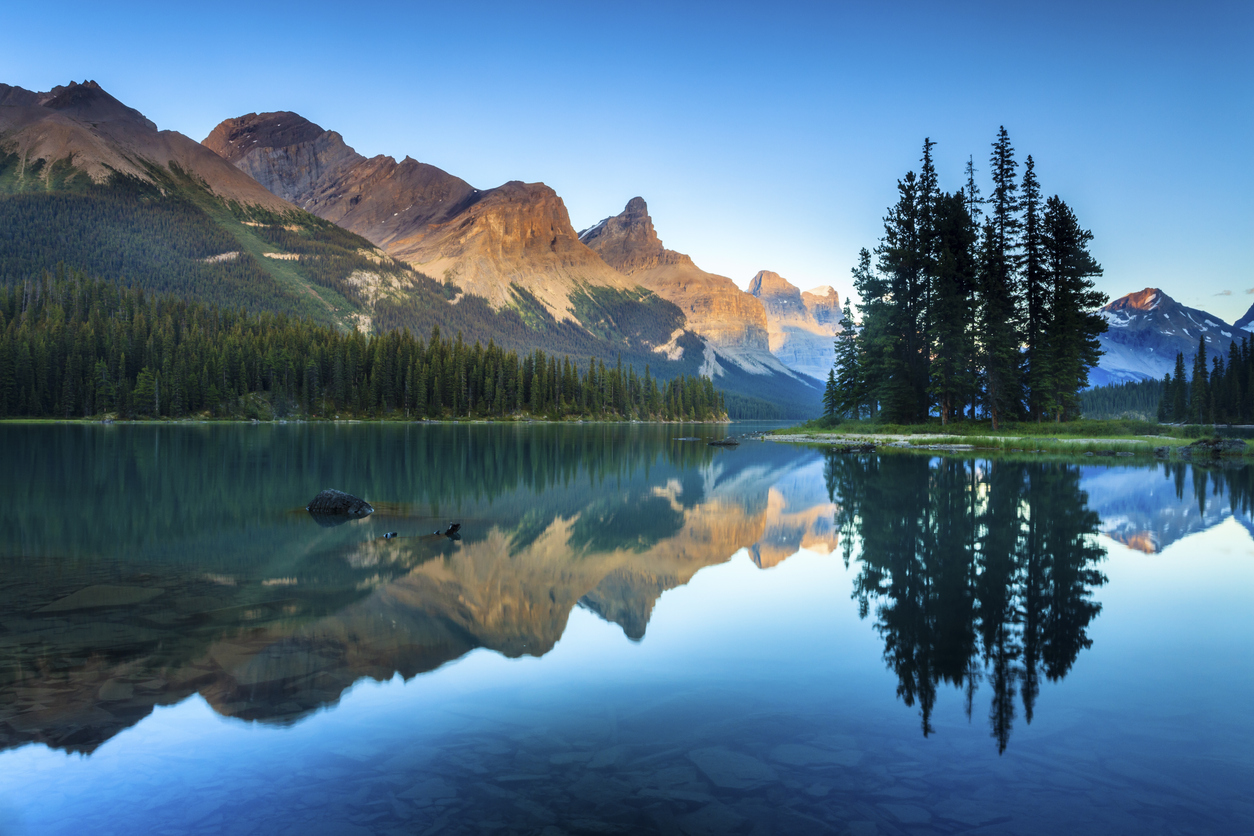
The Benefits of Using a Digital Twin in Automation
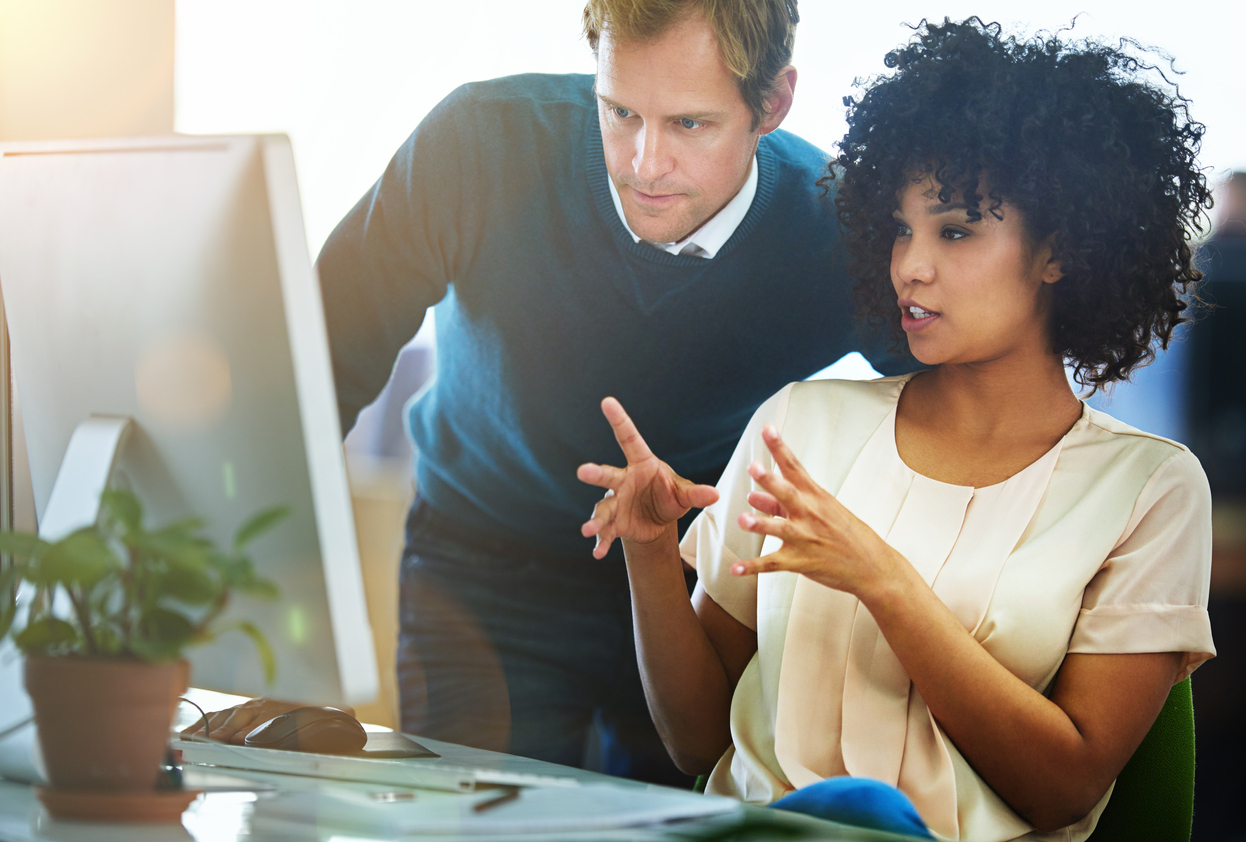
How to Reduce the Rising Costs of RPA Maintenance and Support
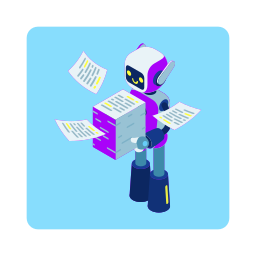