How to Reduce the Rising Costs of RPA Maintenance and Support
According to an EY study from 2019, 50% of RPA projects fail to meet their objectives. One of the biggest reasons why RPA projects “fail” is the level of RPA maintenance and support needed for in-production bots.
Even without quantitative proof from studies like the one above, there is plenty of anecdotal evidence across industries that suggests enterprises are struggling with RPA management. Constant break-fix cycles that require bots to be pulled out of production bring on massive maintenance costs that keep them from delivering on expected ROI. Ultimately these break-fix cycles inhibit the broader business objectives that RPA was meant to drive, like reducing costs, increasing efficiency, and improving process quality.
To understand why enterprise automation teams and RPA Centers of Excellence (CoE) struggle with RPA maintenance and support, it’s first essential to understand why bots break.
Why Bots Break and Need RPA Maintenance and Support
There are three main reasons why bots break or require maintenance:
- Changes to the user interface (UI) of the applications they interact with
- Changes to regulations, policies, or controls that impact the bots
- Missed requirements during the development process
1. UI Changes
Bots routinely break and need RPA maintenance and support as the applications they interact with experience change. For example, a simple bot is designed to automate invoice processing by inputting data into a specific field of an ERP (Enterprise Resource Planning). Over time, the ERP is updated, changing the input field; because of this update, the bot will now produce an error and break.
2. Changing Regulations
Regulation changes are another contributor to high RPA maintenance and support costs. The right RPA management and governance model is something that organizations are still trying to figure out. This is painfully evident when a new regulation or control is introduced or an existing one changes. For the most part, anytime there’s a regulatory change, a manual, time-consuming impact analysis is performed, the bot is pulled off production, modified, tested, and then redeployed.
3. Missed Requirements
Even mature automation teams and RPA CoEs suffer from missed requirements. The reason? Most organizations haven’t found a better method to provide RPA developers with precise and comprehensive bot development guidance. The majority of RPA development work is communicated today through bulky, ineffective Process Design Documents (PDDs) that make it easy to miss requirements during the manual documentation process. It is even easier to miss them when they’re buried in the document itself.
How the Right Upfront Design Approach Can Reduce RPA Maintenance and Support
One glaring issue with RPA maintenance and support is that it’s mostly reactionary. Maintenance of RPA happens when a bot has produced an error, and automation teams scramble to minimize downtime. Yet the diagnostic work necessary to understand where and why the error occurred and then take the corrective actions needed to fix the bot are usually big time-sucks that do little to limit bot downtime.
The key is to transition from reactive RPA management to a proactive strategy with the right design principles. Many RPA maintenance issues and outages are avoidable if you take a comprehensive approach to designing automations and communicating the entire context with precise guidelines to your developers.
It’s crucial to identify every dependency the to-be process has upfront. The more specific, the better—with the right tools, you can connect dependencies to specific, relevant process steps, which provide greater clarity than simply relating it to the entire process. This way, if anything changes, there is a direct mechanism to understand how that system or regulatory change impacts the process and exactly where it is impacted. Vigilantly documenting all dependencies, though, isn’t enough; they need to be explicit and clear to RPA developers, so they’re not missed. Unfortunately, PDDs come up short in that regard.
How Blueprint Helps Reduces RPA Maintenance and Support
Blueprint replaces the PDD with Digital Blueprints to minimize errors and outages for in-production bots. Digital Blueprints contain all the rich context that needs to be communicated to RPA developers, including detailed process flows, functional and non-functional requirements, user stories, compliance and regulatory requirements, and functional and acceptance tests. This context, along with the other critical information in a Digital Blueprint, ensures you can scale your RPA initiatives and minimize rework and maintenance costs. Digital Blueprints are automatically fed into your RPA tool and ensure that your RPA development team has all of this precise guidance and context at their fingertips. Replacing PDDs with Digital Blueprints has led our customers to experience 30% lower bot maintenance costs on average because fewer requirements are missed, and the right bots are built the first time.
Blueprint’s Impact Explorer – a core tool in the Enterprise Automation Suite – enables your organization to establish a proactive change management strategy. In the suite, you trace your to be automated processes to all dependencies. For example, the systems the process touches or the regulations it must adhere to. This means that any time a change is introduced, you can see precisely which processes are impacted and immediately coordinate the preventative measures with your development team to mitigate bot outages and downtime. It’s what has allowed our customers to reduce bot outages by 3x on average.
This is precisely what we presented in our webinar: how to reduce RPA maintenance and support with Digital Blueprints. Watch the on-demand webinar here and discover how your organization can stop break-fix cycles so you can deliver on your RPA objectives.
Share this
Recent Stories
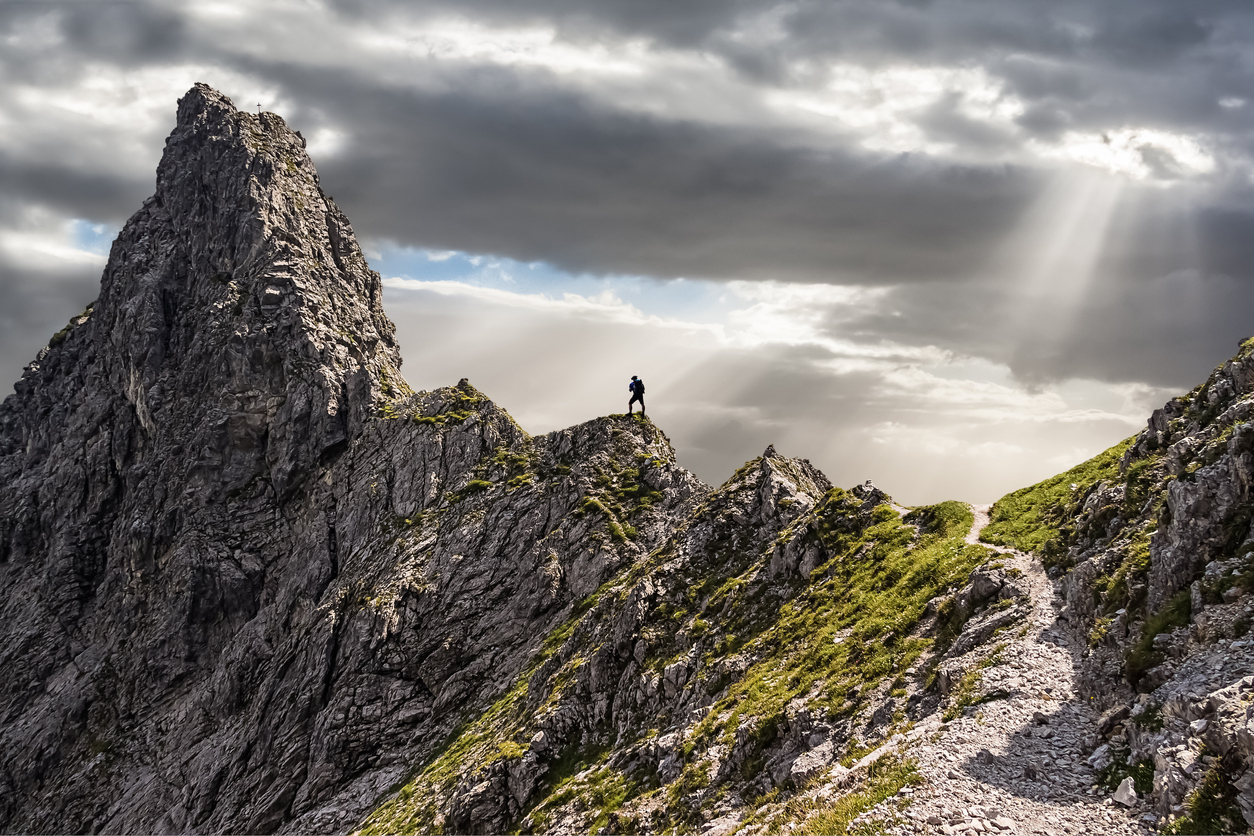
Why RPA Tools Were Never Able to Empower the Citizen Developer
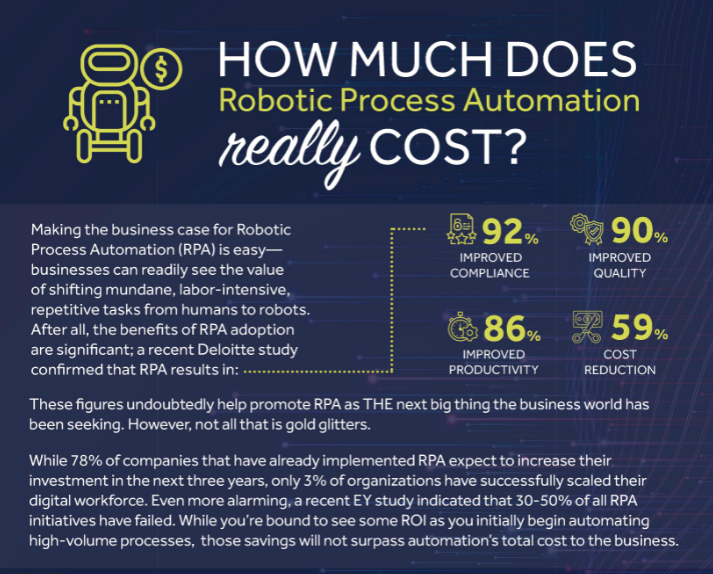
INFOGRAPHIC: How much does Robotic Process Automation (RPA) Really Cost?
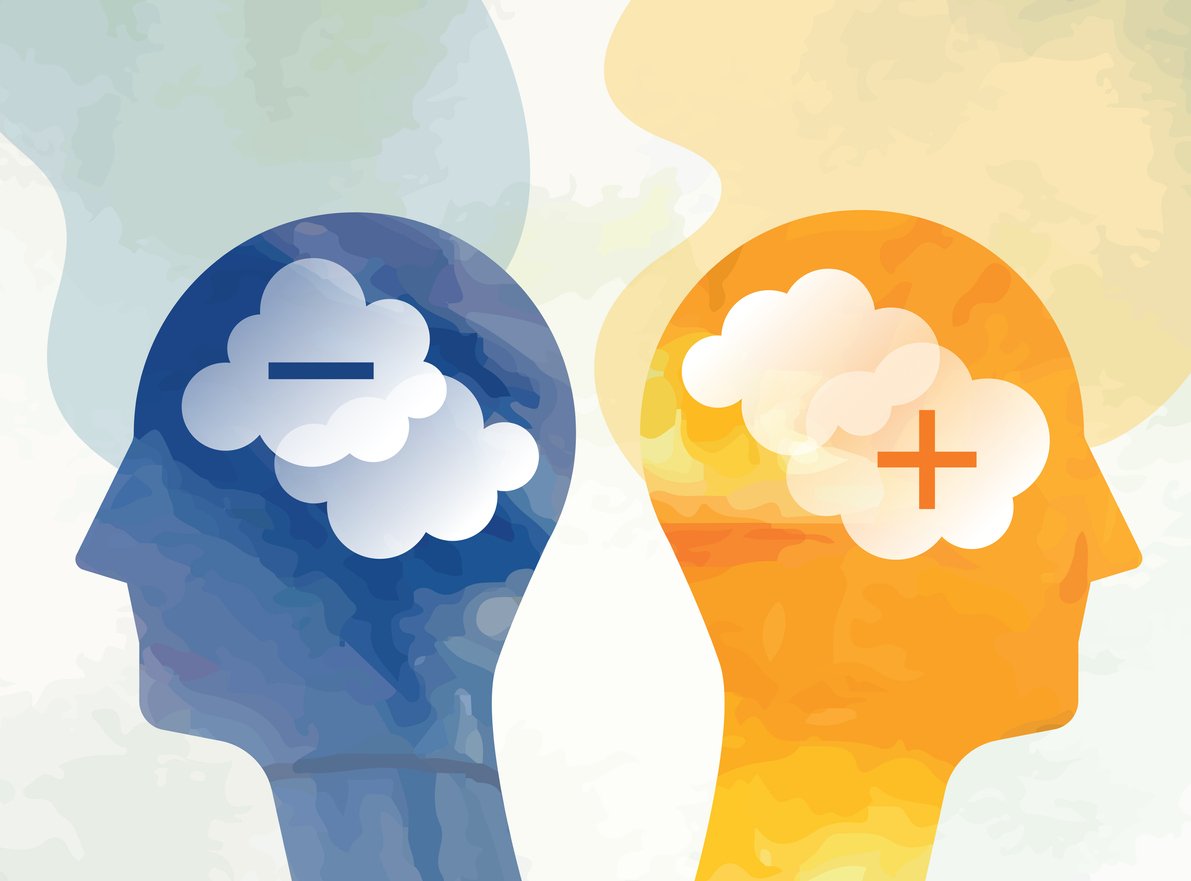